Chain tensioner innovation
Last updated: February 16, 2025
Summary
- The chain tensioner of the Supre Drive is not just innovative in being separate from the derailleur, but also by having hydraulic damping and producing constant chain tension.
- The cable connecting the tensioner arm to the spring is what enables the constant chain tension. In contrast, conventional derailleurs produce a lot more chain tension in the low gears which pointlessly adds drag.
- The damper is hydraulic. This makes it effective at stabilizing the chain without affecting shifting. Also, it’s highly durable because there are no sliding surfaces wearing out like in the “clutch” damper of conventional derailleurs.
The chain tensioner of the Supre Drive is separate from the derailleur. In conventional derailleurs, the spring and damper have to fit in the knuckle of the derailleur. By relocating the chain tensioner to the middle of the bike, we not only give the derailleur ground clearance but we freed ourselves to improve the chain tensioner in ways that aren’t possible with conventional derailleur drivetrains. Read on to find out how the chain tensioner of the Supre Drive works and what makes it better.
[videos of chain flopping around on conventional derailleur drivetrains and on the Supre Drive]
Chain chaos
The forks on shocks on mountain bikes stabilize the motion of the rider. Similarly, the chain tensioner stabilizes the motion of the chain. In the knuckle of conventional derailleurs, there’s a torsion spring that pulls on the tensioner arm (or cage) to keep the chain taught. There’s also a damper which is commonly referred to as a clutch because it includes a one-way clutch that makes the damping happen in one direction only. Forks and shocks have different amounts of damping in each direction of motion, but chain tensioners only need damping in one direction to do their job.
To understand how the chain tensioner of the Supre Drive works, let’s look at how it was developed. The basic idea with the Supre Drive is to relocate the chain tensioner from the derailleur to the middle of the bike. The chain tensioner arm pivots around the bottom bracket shell.
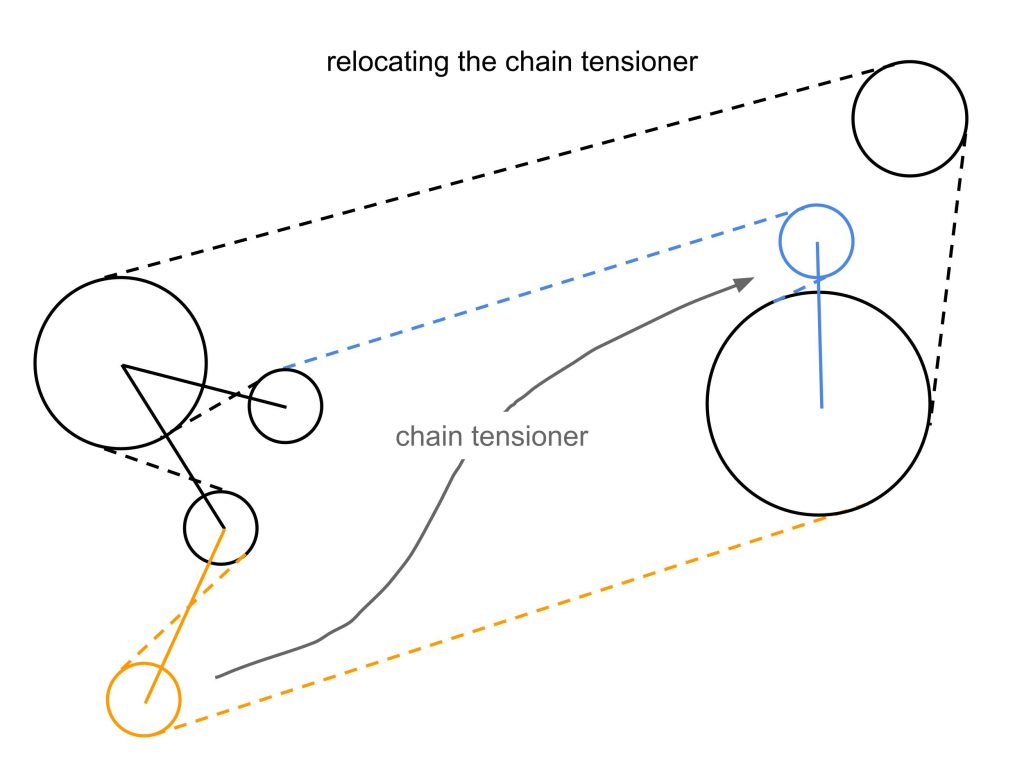
Spring and damper
The spring and damper were relocated along with the pivoting arm and pulley. In early versions of the Supre Drive, the damper and spring were integrated into the tensioner arm and concentric with its pivot axis—in other words, the spring and damper were around the bottom bracket shell as part of the tensioner arm. The illustration below compares this with a simplified representation of the spring and damper in conventional derailleurs.
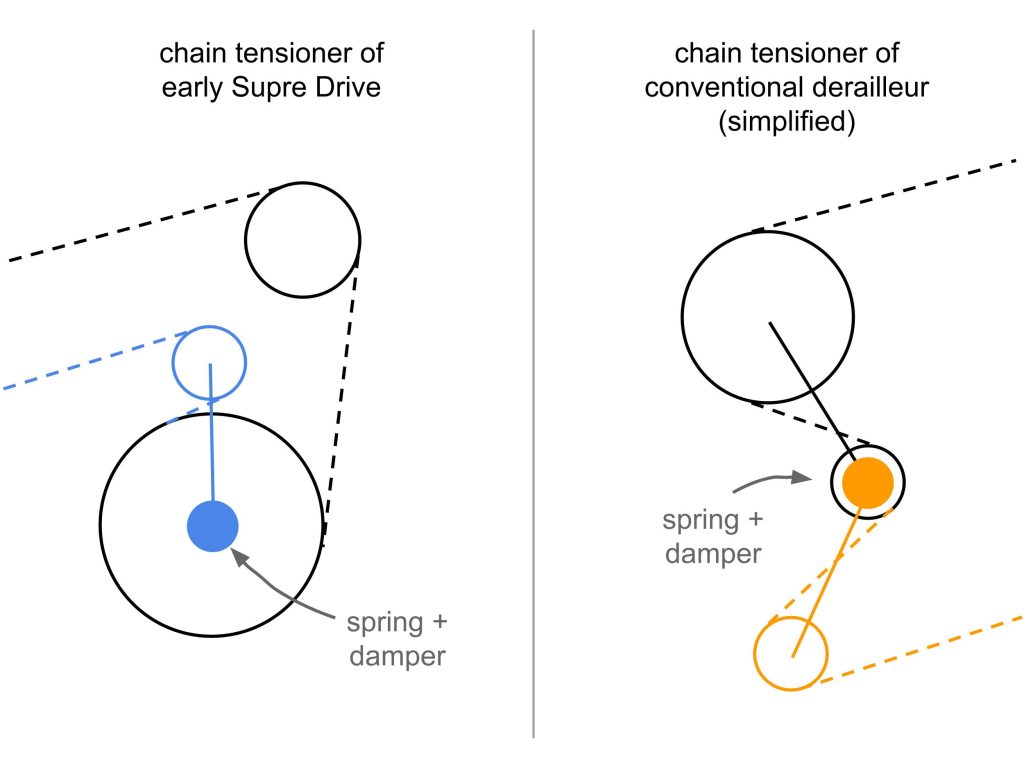
Constant chain tension
While building and testing early prototypes, Cedric invented a way to make the chain tension constant throughout the range of gears. When conventional derailleurs are downshifted toward the granny gear, the torsion spring winds up as the tensioner arm (cage) pivots. This results in a roughly 50% increase in chain tension. This is undesirable. Ideally, the chain tension slightly decreases because there’s less need for chain stability when slowly winching up a hill. The breakthrough idea for achieving constant chain tension is to separate the spring from the chain tensioner arm and to connect them with a cable.
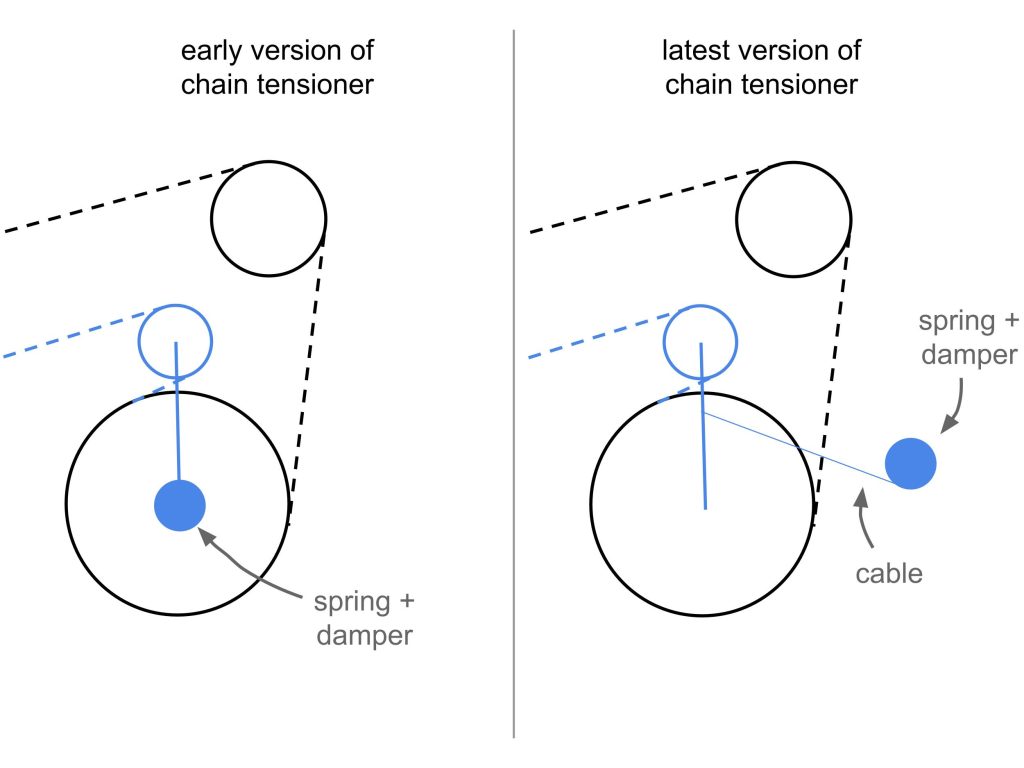
When the tensioner arm pivots backward, the leverage of the cable on the tensioner arm decreases while the force from the spring increases. These changes cancel out, resulting in constant chain tension.

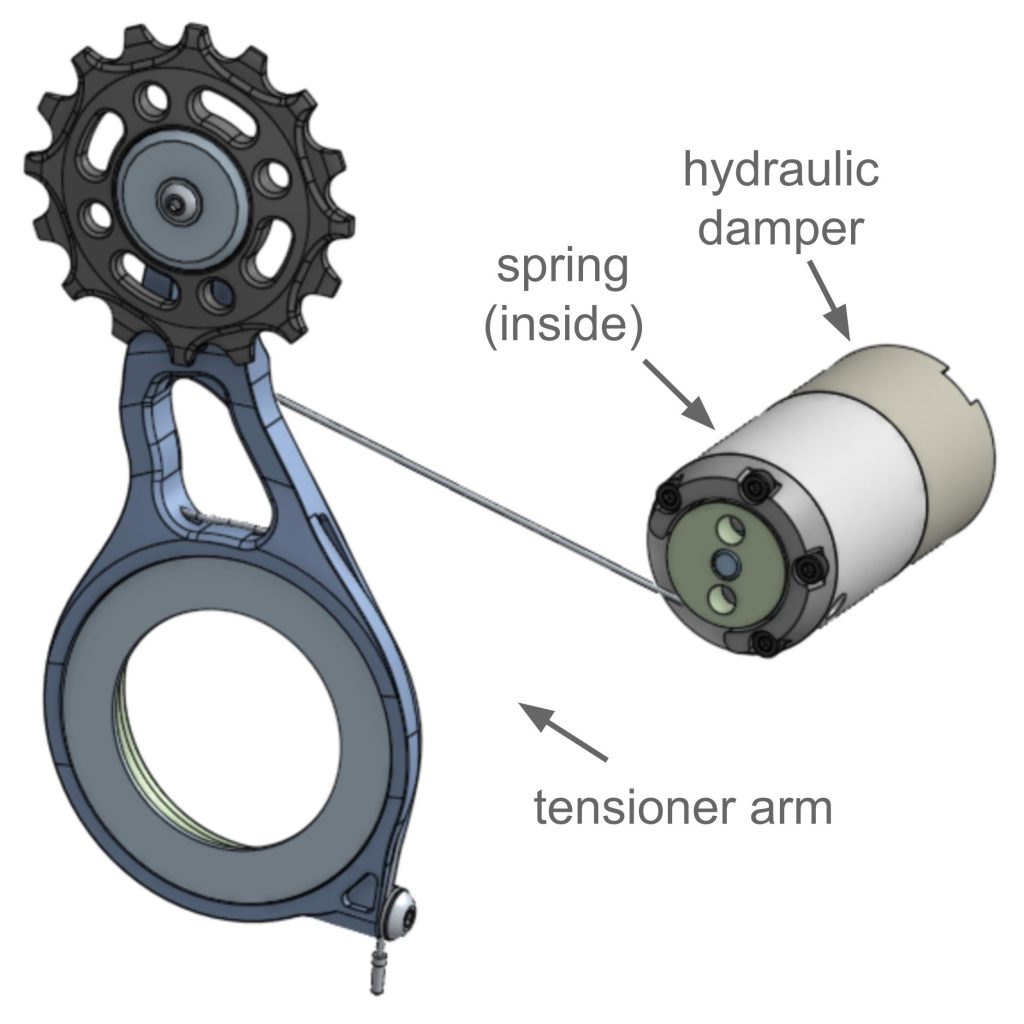
Here’s a 3D model of our chain tensioner so that you can see what this cable system actually looks like. The cable is a regular shift cable. The spring and damper are part of a compact unit that we call the chain tensioner cartridge. The spring and damper are well-sealed from the external environment so that they never need to be serviced.
Hydraulic damping
The spring produces a certain baseline chain tension (around 1kg of chain tension force), and the damper adds extra chain tension to stabilize the chain when it’s getting wild. In conventional mtb derailleurs, the damper (clutch) works with sliding friction. This means that it dissipates energy by sliding two surfaces against each other. This friction converts the motion energy of the chain into heat. In the chain tensioner of the Supre Drive, the damper is hydraulic. The chain motion energy is also dissipated by friction, but instead of sliding friction, it’s viscous friction in a liquid. By forcing oil through a small passageway, there’s friction within the oil between all the little liquid molecules.

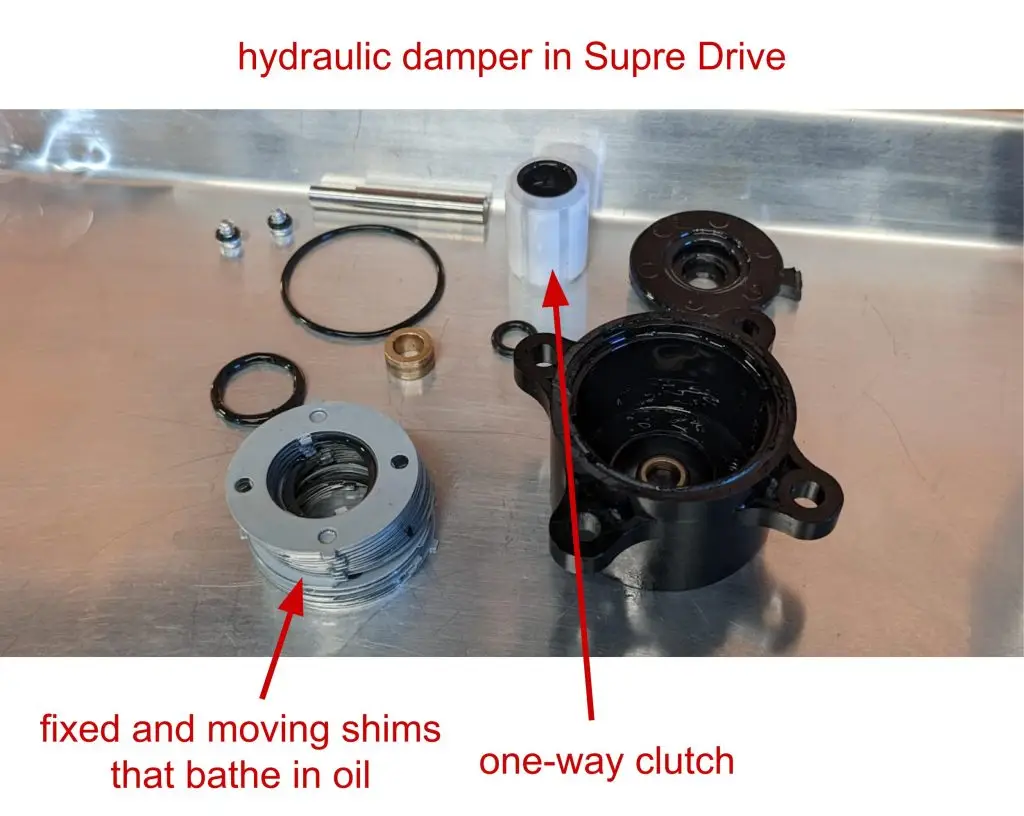
Another advantage of hydraulic damping is its speed dependence. Ideally, there would be no damping when shifting gears so the damping doesn’t interfere with the shifting, and there would be a lot of damping when plowing through rock gardens so that the chain is stabilized. With sliding friction, the opposite of this happens—there’s stiction that creates more damping when shifting gears, and sliding friction inherently produces less force when the sliding speeds up. Hydraulic damping is inherently speed-dependent so that there’s less force at low speeds and more force at high speeds, just like we want. A good analogy is walking versus running waste-deep in water—unless you’re Jesus, you probably experienced the resistance go up dramatically when you tried to run in water.
Now you know how our chain tensioner works and why it rocks. It’s durable, it’s hydraulically damped, and it produces constant chain tension.
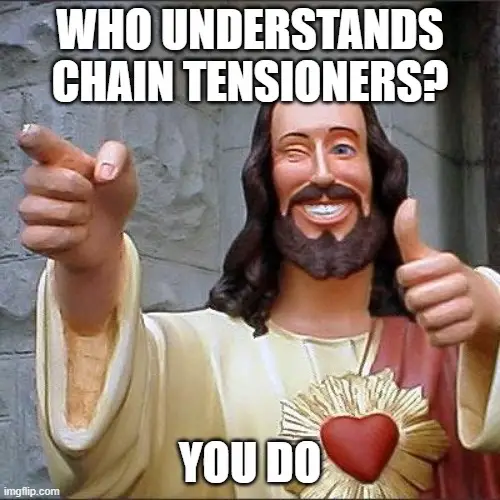