This is an open-source project (MIT license). Anyone can use the info here to make their own DAGR.
DAGR
(Derailleur Alignment Gauge Repurposing)
The DAGR works by using fork stanchions as the reference point for aligning handlebars. It’s clamped to stanchions, and then a derailleur alignment gauge is attached to the DAGR. The user then touches off on both sides of the handlebar to check for straightness. Because of its self-centering mechanism, the DAGR tool centers the derailleur alignment gauge so that the user touches off on the same spot on either side of the handlebar. The DAGR works with narrow non-boost XC forks all the way up to Fox 40s.
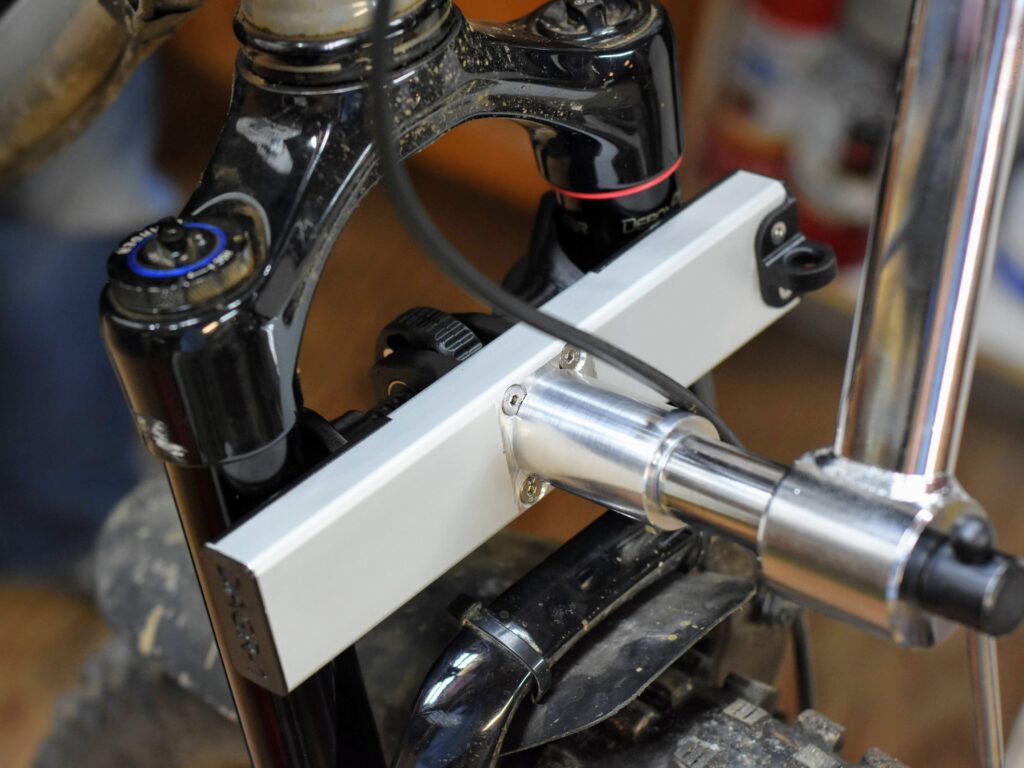
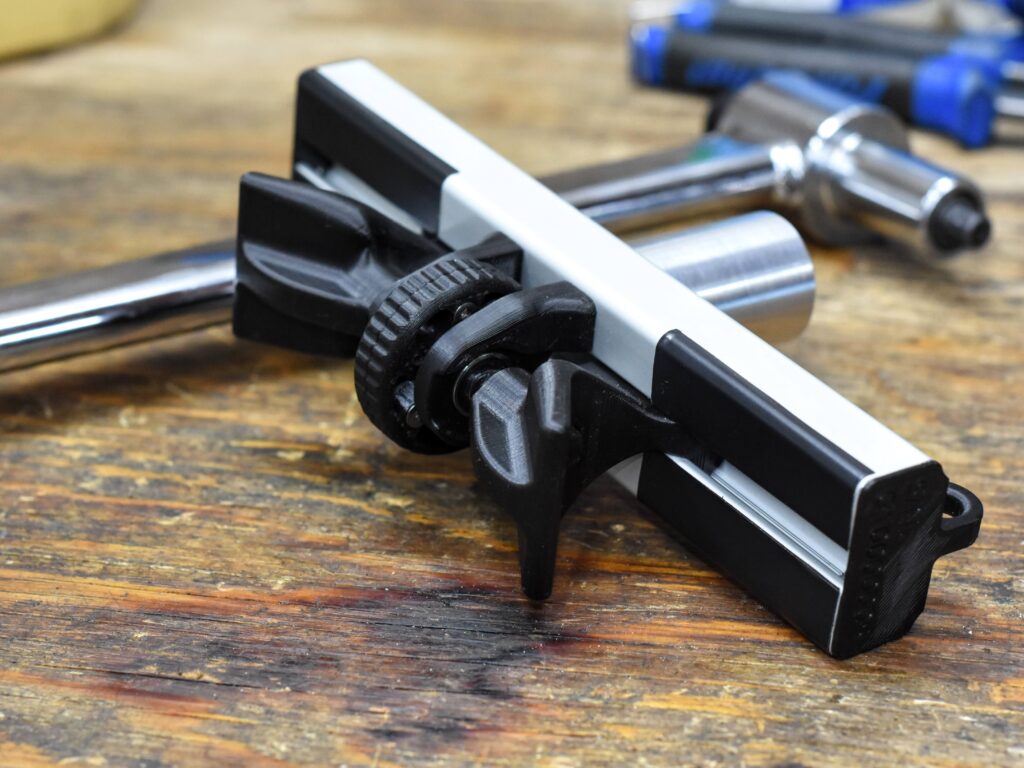
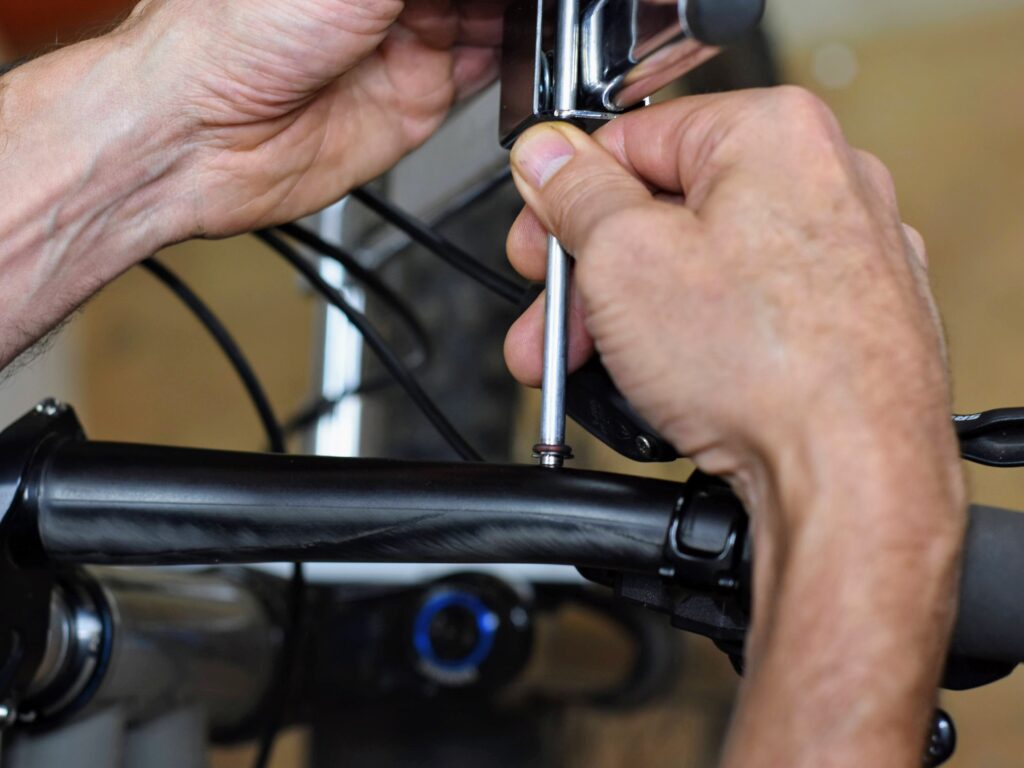
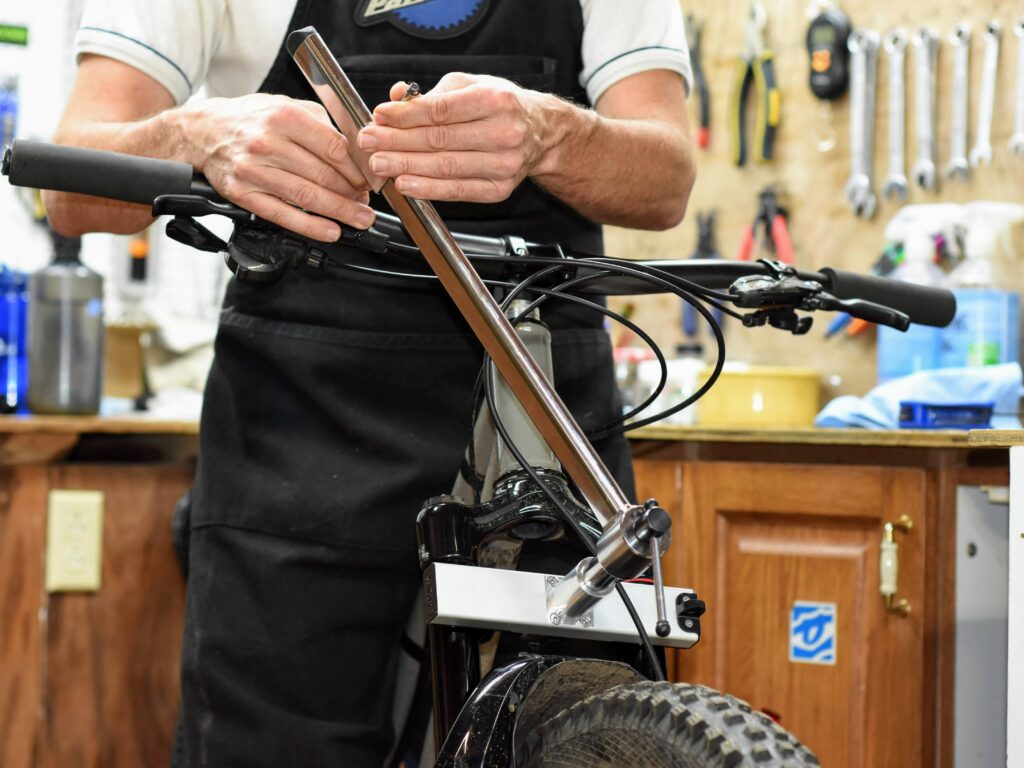
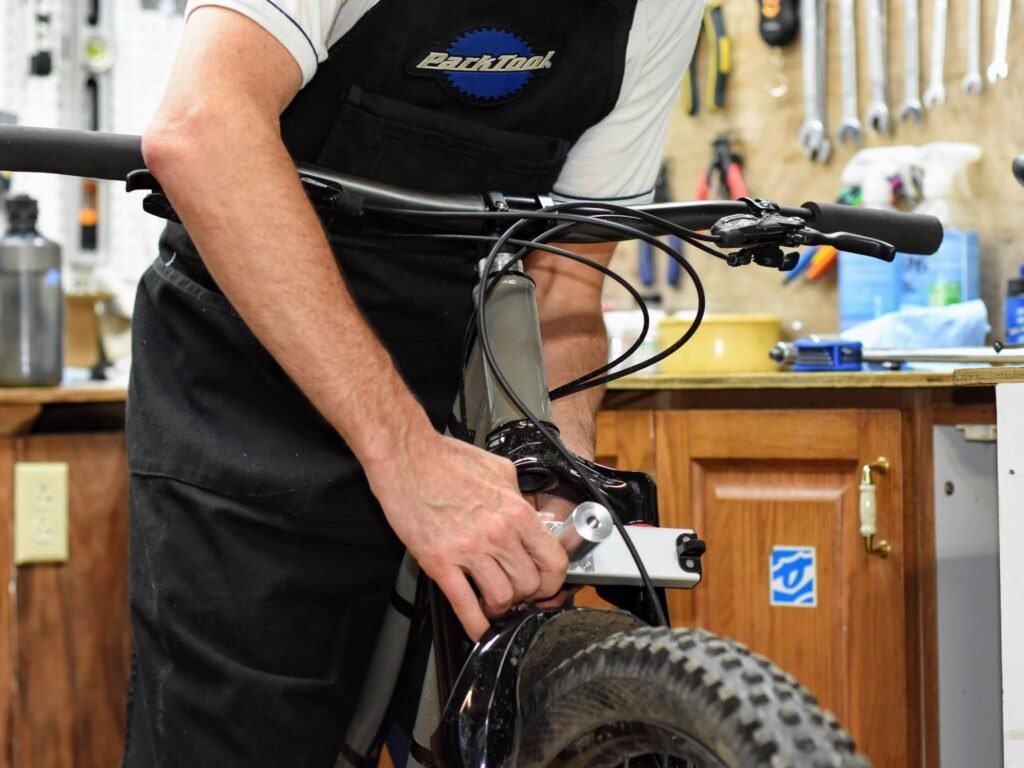
BENEFITS
Peace of mind: No more wondering half way through your ride if your handlebar is straight.
Quick & easy: The alignment process is quick and takes less mental effort than the eye balling technique.
Brake lever alignment: Also useful for matching the position of brake levers.
Purpose for your DAG: The DAGR gives a new purpose for your derailleur alignement gauge, which might otherwise be rendered obsolete by our drivetrain.
WHAT THEY SAY
FABRICATION
Link to bill of materials spreadsheet
Link to Onshape document with 3D model
Click the link above to access an Onshape document with the 3D design of the DAGR along with engineering drawings. To get the models to 3D print, go to the “3D prints” tab, and then right click on the parts in the parts list (lower left) and export to stl. For the drawings, you can right click the tabs (“T-slot extrusion” and “extension”) and click “Export…” and select the pdf format.
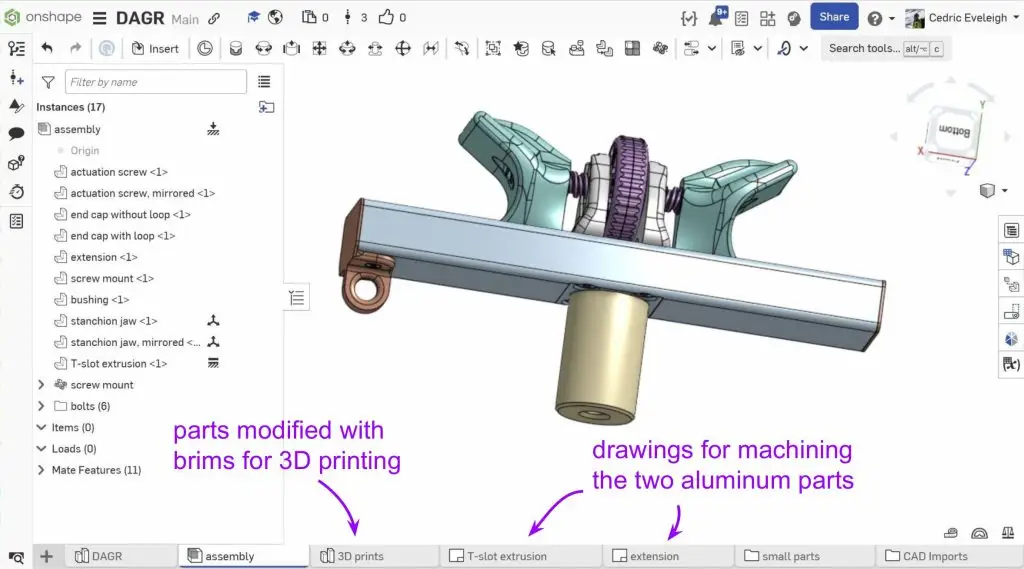
The two aluminum parts can be machined with common machine shop tools, except for the thread of the extension which is M18 x 1. However, if you don’t have an M18 x 1 tap and die, this part can be redesigned with a different thread size. The reason we went with M18 is so that the extension can be machined in one setup in the lathe, which matters more for mass production than one-off manual machining.
We print the plastic parts with 100% infill (solid) and with PC Blend filament (polycarbonate with additives). Printing with polycarbonate requires an enclosure. It’s more difficult to print with than common materials like PLA and PETG, but it’s very tough, which is important for something that will get beaten up by bike mechanics.
If anything’s not clear, let us know (contact page).
The DAGR was invented and designed by Cedric Eveleigh. For those who are interested, here’s a link to a patent that was granted for the DAGR (the patent is granted, which confirms the novelty, but it’s abandoned and therefore inactive).